Varnished AW Hydraulic System Fluid
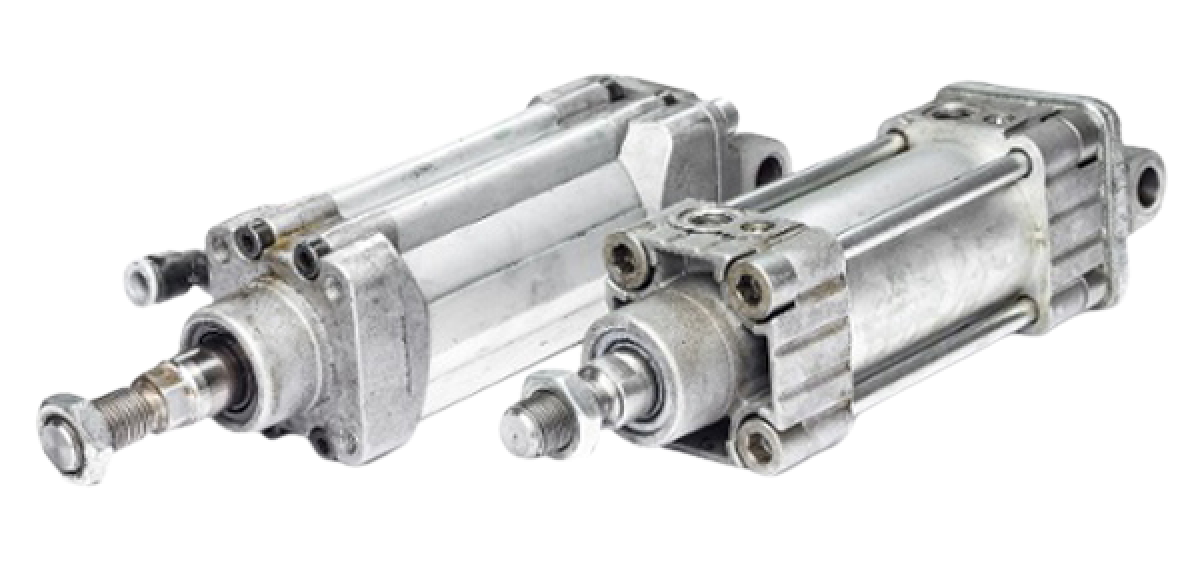
Varnished AW Hydraulic System Fluid
Find out how we helped a refrigerator manufacturer save over $200k a year by removing varnish from their hydraulic system to reduce downtime, defective units, idle labor and maintenance costs.
In the process of manufacturing refrigerators, isocyanate is hydraulically injected into the body of the appliance to improve insulation. After injection, the chemical transforms from liquid to foam. For one company, this created an issue where small amounts of isocyanate were adhering to the hydraulic cylinder, which would then introduce the chemical to the AW hydraulic fluid. Portions of the isocyanate would dissolve, causing varnish deposits and gels to form, while the remainder would remain solid, becoming particulate contamination.
These high levels of particulate (22/21/16) and varnish contamination (MPC∆E = 33.1) were causing excessive amounts of product defects and downtime due to premature equipment failure of pumps, motors, and actuated control valves. In addition, hydraulic pump motors were operating at 150% of their maximum rated current, reducing service life and generating heat that increases system susceptibility to varnish.
To slow the buildup of varnish, oil was changed biweekly. Per the injection system manufacturer, ISO Fluid Cleanliness Codes above 21/18/15 void the warranty of the system and its components. (ASTM D7843 indicates that MPC∆E levels should be less than 15 to prevent harmful varnish deposits and gels from forming.)
The company turned to Bennett Filtration for help. Our team installed an FSW offline filtration unit to effectively remove varnish and particulate contamination and upgraded the hydraulic pumps and motors to normalize fluid temperature and curb varnish susceptibility.
The results showed significant improvements: ISO fluid cleanliness showed particles had reduced by 93.5% to 18/15/10, while MPC∆E dropped to 5.2 (84% reduction). Annual defective units decreased by 408, eliminating 16.81 idle labor hours due to downtime. Substantially reduced varnish buildup negated the need for frequent oil changes, saving over $200k annually.